About MEBAC
Metal Slip-Resistant Surfaces
IKG’s MEBAC® slip-resistant surfaces are manufactured to provide the absolute best in safety.
Produced using a proprietary arc spray process, IKG provides a best-in-class, slip-resistant surface that is uniform and extremely durable. MEBAC slip-resistant surfaces are fast becoming a critical part of many companies’ safety programs.
Unlike other anti-slip coatings, MEBAC surfaces are not made of tape, resin, or paint. Instead, molten metal is sprayed onto the surface and a grit media, available in different sizes for different applications, is then encapsulated with additional coats of the molten metal.
MEBAC slip-resistant surfaces have been in use for over three decades worldwide and are produced at our EPA compliant facility in Leeds, Alabama. MEBAC is available through our nationwide network of sales and representative offices.
IKG is the industry-leading supplier of strong, durable grating products for almost any industrial use. Our products’ safety performance is greatly enhanced by the application of MEBAC anti-slip coatings. MEBAC is a durable, zero-maintenance coating that can be applied to IKG bar grating, metal plate and customer-provided material, providing many years of top-performing slip resistance in protected areas.
MEBAC is the original anti-slip coating.
Unlike competitor coatings, which are comprised of tape, resin or paint, MEBAC anti-slip coatings are produced using a proprietary arc spray process. Molten metal is sprayed onto the surface with a special grit media encapsulated with additional coats. The result: a best-of-class, slip–resistant surface that is uniform and extremely durable under dry, wet, and oily conditions.
Available in different sizes and options, MEBAC coating can be utilized for a wide range of applications, from walkways to distribution center storage systems to heavy-duty roadways, airports, and bridge spans. In any environment where liquids are handled, stored, or transported and where there is heavy foot or vehicular traffic, MEBAC anti-slip coatings provide margins of safety that are unmatched in the industry.
MEBAC coated surfaces have been in use for over three decades worldwide and are available through IKG’s nationwide network of sales and representative offices.
Importance of Coefficient of Friction
A coefficient of friction factor of 0.50 is considered by OSHA to be a safe surface on which to perform work. The American Disabilities Act suggests a factor of 0.60 for a flat surface and 0.80 for an inclined surface. MEBAC meets or exceeds these requirements to provide a safe flooring option for any application.
How MEBAC Works
MEBAC anti-slip coating provides a consistent, safe surface in areas of heavy foot traffic where common workplace activity can lead to slips and falls.
MEBAC products are manufactured using abrasive grit particles encapsulated in a metal spray arc that is bonded to an aluminum or steel substrate. MEBAC slip-resistant surfaces offer a consistently high coefficient of friction under a wide range of conditions, even if the surface is subjected to water or lubricants, providing margins of safety that are unmatched in the industry.
Since MEBAC can be applied to virtually any steel or aluminum substrate chosen by the customer, the design engineer has maximum flexibility in selecting the optimum components to complete the required job. For a complete view of coating, surface, and material options, view our range of MEBAC coating options. Plate sizes are available in standard sizes or can be custom fabricated for a specific application. Where installations can utilize standard plate sizes, view the load tables in our downloads area for further information.
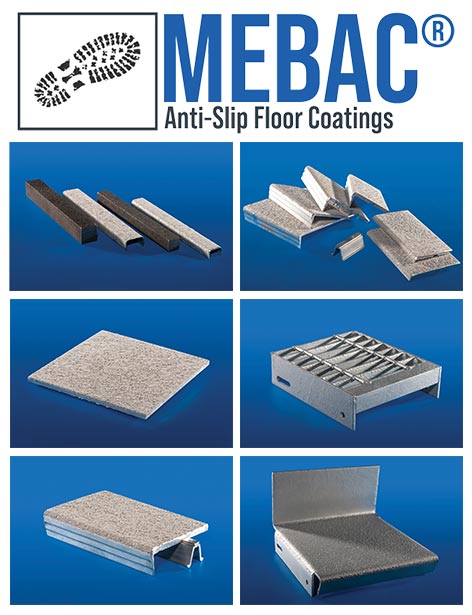
MEBAC Physical Properties
Durability
MEBAC’s durability is the result of bonding and exceptional wear resistance. Since the aluminum oxide grit particles are an even harder substance than the metal arc spray encapsulating it, any eventual wear of the metal surface simply serves to expose an even tougher wearing material.
Strength
Although MEBAC slip-resistant surfaces have no load carrying capacity of their own, tests have shown that a MEBAC surface acts in composite with the metal substrate. Nevertheless, our plate thickness dimensions do not include the thickness of MEBAC coating.
Technical Data
Uniformity
Other abrasive metals processes are unable to control grit dispersion, resulting in some surface areas with too much grit and some with little or none. MEBAC®’s unique manufacturing process yields a consistently uniform grit pattern.
Tested Bond Strength
Steel coating to surface
5,582 PSI
Aluminum coating to surface
5,911 PSI
Surface Buildup (added weight to substrate)
Steel
= .89# / sf
Aluminum
= .36# / sf
Tolerances
Stock sheet sized material
Standard mill tolerances will apply (generally slightly oversized)
Fabricated Plates
+ / – 1/8”width and length, and ¼” square
Fire Resistance
Ignition Plus Combustion Time (min.)
4.25 Max (specified) / 0 (actual)
Average Char. (in.)
6.00 Max (specified) / 0 (actual)
Food Approval
FDA approved and USDA approved (aluminum EZ weld)
Surface Buildup (added weight to substrate)
Tolerances
– MEBAC is applied to horizontal surfaces only.
– Maximum width of coated material = 60”
– Maximum length of coated material = 240”
– Maximum height of coated material = 8”
Advantages of Using MEBAC
Safety
The most important advantage should always be safety! No other product can exceed MEBAC’s consistently high results for coefficient of friction under a wide range of conditions. Even when subjected to water and lubricants, MEBAC slip-resistant surfaces meets OSHA’s standards for a safe working surface. Why would you want employees or the public walking on any other slip-resistant surface?
Economy
Although the initial in-place cost of MEBAC may be somewhat higher than other types of anti-slip surfaces, it is much more economical over the product’s life. Unlike other anti-slip products, that may need to be reapplied to the surface over time, MEBAC is applied only once during fabrication; it does not need to be reapplied saving additional labor and material cost. Plus, potential indirect costs and expenses are lower due to decreases in slip/fall accidents, lost man hours, and equipment downtime.
Fabrication Flexibility
MEBAC coatings can be applied either before or after fabrication of metal components.
However, it is recommended that whenever possible, bending or forming of substrate should take place before applying MEBAC. Also, when holes, cut-outs or attachments are performed on plain plate, they yield a higher quality, lower cost and avoid the excessive tool wearing, uneven cut, abrasive edges and scrap that can occur on a surface that already has a MEBAC coating on it.
Fabrication after MEBAC has been applied is feasible and the fabrication tips offer practical guidance if post-coating fabrication is required. See the downloads section for more information.
Availability
IKG’s MEBAC production cycle is short enough that manufacturing lead times rarely exceed three weeks for standard material, and are more commonly between one to two weeks depending on shop cycle time.
History of the MEBAC® Brand
The history of thermal spray goes back the better part of a century. Fuel air thermal spray dates to around World War One, but it was not well suited for non-slip applications. Electric arc thermal spray was invented in Europe in 1945, and made its way to America soon afterwards.
Maximilian Palena invented MEBAC in 1963. He was part of Plasma-Spray Corporation in Cherry Hill, New Jersey, at the time. The US Navy contracted Plasma-Spray to research methods of treating aircraft carrier jet blast deflectors. The coatings had to be corrosion-resistant, durable and slip-resistant. His work was inspired by a research paper called New Developments in Plasma Arc Weld Surfacing which was presented by R. Zuchowski and E. Garrabrant at the 1963 American Welding Society’s 44th annual meeting. Mr. Palena conducted dozens of careful tests to find the correct settings and sequences to produce a product to meet the navy’s specifications.
The US Navy continued to test the early MEBAC products until at least 1975 (12 years after Plasma-Spray first started research into this area). A report from the US Navy at that time credited what was later to be called MEBAC as being the best product available for their application after tests onboard the USS Kitty Hawk. It is unknown if the Navy ever did actually buy flooring from Plasma-Spray. However, in 1968, Mr. Palena filed for a patent entitled Metal Bonded Non-Skid Coating and Method of Making Same. It was granted in 1975 as patent number 3,855,444. Around this time it is presumed that Plasma-Spray began to commercially produce this product in a plant in Pennsaoken, New Jersey. Later, in 1976, Mr. Palena filed for another patent (entitled Metal Non-Skid Coating) that was a refinement of the earlier patent. It was granted in 1977 as patent number 4,029,852. The spray heads and wire drives were homemade from Plasma-Spray’s design. Although other companies began to produce off-the-shelf commercial units, Plasma-Spray has largely retained the original design for the spray heads.
In the 1970’s IKG became interested in MEBAC and initially bought the plant in New Jersey prior to 1979. At this time only aluminum MEBAC was produced.
In 1984 the equipment was moved to Nashville along with one or two of the operators from New Jersey. Steel MEBAC was introduced in 1985. In 1986 steel MEBAC began to be hot-dip galvanized although it was known that there could be issues if it was not pickled correctly. During this time, Mr. Palena received royalties on all MEBAC produced, but apparently was not involved in further product development.
In the 2000’s, a truly effective dust collection process was applied to the equipment for the first time. There were various improvements in wire feeding, blasting methods, standard operating procedures and preventative maintenance. For the first time, effective quality measurements were put in place. At this time the plant discontinued hot-dip galvanizing in favor of aluminum coatings. Successful experiments in spraying a galvanized product were conducted, but shelved in favor of aluminum. Stainless steel coatings were experimented with, but remained elusive as a viable product.
Our most recent move was to Leeds, Alabama in 2005, where we developed a partnership with Valmont Galvanizing. This enabled IKG to offer a steel-on-steel, hot dipping process to the general market without fear of product failure. In 2014 IKG purchased new equipment to keep up with technology, with a new blast cabinet and PLC-controlled coating house.